Building An Officer and a Gentleman The Musical
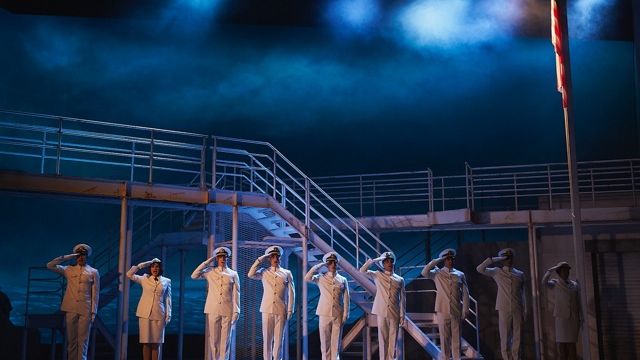
Building a set for a multi-million dollar musical is a big journey. Even more so when it is a world premiere of a production set in part on a battle ship. Technical Director Nick Eltis discussed the journey from set designer’s drawings to the massive, automated steel set with Neil Litchfield just ahead of the show’s first performance.
With the musical closing early, on July 1, and the tour cancelled we bring you this article, intended for our July / August 2012 magazine.
Neil Litchfield: What is your job of the Technical Director?
Nick Eltis:To make sure that what the designer comes up with (a) we can build, and (b) we can make it fit into the various venues which was a big thing, particularly with a set of this size, making sure it can fit into the venues. It has to fit into a number of venues, not just this one. Making sure that it can be built into pieces that are small enough to handle, and bolt together. It needs to be engineered to ensure that it’s structurally sound, and also integrating all of the other departments, not just the set and staging, but getting sound and lighting and whatever we’ve got integrated in, so it works together.
NL: And I suppose there’s an OHS element as well.
NE: A significant part of the consideration we give is how we can make it as safe as we can. It’s big, and heavy, and steel, so there are lots of potential dangers.
NL: What was your first step when you became involved as Technical Director?
NE: I spent a day with the designer looking at the model. Seeing it in drawings is one thing, but getting an understanding of how he envisages it working is an important part of it, because it lets you understand what you can change and what you can’t. There were some parts which we had to change because we just couldn’t build them, or they weren’t practical, and getting an understanding from him as to what the essential elements were. There were some parts which we had to change because we just couldn’t build them, or they weren’t practical.
NL: What were some important early changes or inputs that you made?
NE: We chopped the height of the set down by just under a metre, and we made the show deck smaller so that it could fit in all the venues. We discovered was that there were old drawings of one of the venues floating around that were incorrect. We worked in that venue last year, and we had accurate drawings. We made it a bit buildable as well. There were some things that just weren’t practical in the build – the size of things, some staircases that if you did them the way they were originally drawn it would be almost impossible to climb them. There’s lots of little things, but also, there a lot of ‘OK, you want this to be automated, how are we going to figure out the best way to do that.
NL: Going down the journey from that meeting?
NE: I then had someone take the designer’s drawings, and clean them up. We put it out to tender, selected a contractor, then spent a few weeks working through the detail of building it with that contractor. Again, they made some suggestions about modifications to make it easier and more affordable to build. Then they start drawing it for construction, and we approve every construction drawing before it goes to fabrication.
NL: So how was the construction phase?
NE: It was very rushed. We didn’t have a lot of time to build this but we were fortunate with this one. We contracted the set constructors to get a warehouse and do a test build. Everything up to about five metres off the ground had been put together before we got to the theatre, which was invaluable – being able to have it built, and prove that everything lines up and everything works, and you’re not in the theatre trying to endlessly drill out holes that don’t lie up, was invaluable. Between them and my associate they drew everything on this set – every last bolt is in the drawing – so they knew that it was going to work before they put it together. And it went together almost seamlessly.
NL: So that allowed a smooth bump-in into the theatre?
NE: Very. We finished constructing ahead of schedule and under budget. There have been ongoing changes – it’s a new show, so there are lots of little things, as the creative team look at it and start to use it and play with it. Some are as simple as change the colour of this piece, to no, actually we don’t want that whole thing anymore. We’ve added pieces of steel, and pieces of mesh, and handrails, and things here and there.
NL: At what stage did you put actors on it?
NE: We spent a bit less than two weeks building it – we lost a few days to public holidays. Then we spent five days dry teching it, so that we knew everything worked before the actors got here. Then we’ve spent a bit over a week teching the show with the cast. And it’s all going swimmingly – no catastrophes yet.
NL: Have there been any interesting changes or challenges once the cast started using the set?
NE: A lot of traffic issues. This is a very busy show backstage. We’re trying to do everything here as though we’re doing it in Melbourne, which is the tightest theatre we’re going into. Once we get to Her Majesty’s it’s a very tight space.
In general they’ve been OK. On Day 1 we spent a lot of time taking the cast over every inch of the set. We walked them through the whole set individually, and pointed out all the things they can hurt themselves on. That took a long time, but it’s a very important part of the process, particularly with something like this, where it’s elevated and there are openings at height that they need to be very conscious of.
NL: There are a lot of training exercises that take place on this set as well.
NE: One of the central elements of the story is the candidates getting through the traning. There’s a climbing wall, which is a standard military training – they have to get up a climbing wall with a rope. We had to figure out how to build that into the set, so it’s there and not there. We built a training wall for them that replicates the height and size, using exactly the same material as the actual climbing wall, that they can train on out the back to their hearts content to get their body strength up. I mean I can do it once, but I can’t do it twice in a row. It’s hard work on their upper body, and it uses unusual muscles for them. There’s climbing ladders and tyres they run through and push-ups – lots of physical stuff that I just can’t do.
NL: How did that get integrated into the set?
NE: The central staircase has a piece of mesh on the side of it that’s slightly different to all the other bits of steel mesh you can see in the set. It’s a heavier gauge mesh, so it’s much stronger, so that when they are climbing against it and bashing against it, it withstands that. There’s lifting points on the other side of the staircase, so that we can attach the climbing rope. That particular handrail is stronger than all the other handrails, so it can handle that weight going on it, and then the whole central staircase is on a steel plate to transfer the load through the floor so that it doesn’t topple over when there’s two people climbing on the front of it.
That was one of the engineering challenges, because one of the artistic requirements was no diagonal bracing for any of the support legs for any of the set. Normally as soon as you talk engineering you need triangles, because that’s what makes it strong, and we’re not allowed to have any of them in the design. So that was difficult to get that right.
NL: How did you achieve it?
NE: It’s mostly about the wall thickness of the steel – how heavy it is. It’s all hollow steel. They’re bolted to a steel plate, to give more attachment points to the floor, to help distribute that load. We were fortunate that we had a full 3D model of this, which helped the creative team understand where they could fit things. We’re with the construction company every day, making sure that it’s right. Then we get to the theatre we start bolting it all together. But before that, we work with the lighting and sound designers to make sure their facilities are catered for; that we can fit the lights, that we’ve got holes for smoke to come on stage, and all that we do all that as part of the drawing process as well. And then we build it.
NL: And adding the sound and light?
NE: The lighting and sound guys, as part of the build process here, are scheduled in parallel with the set build. In this one, because of the towers on either side, once those towers are up we can’t drop the lighting bars in to the stage floor. So it has to be done in the right order, and we set aside time for those guys to program and focus, and the sound guys need to tune and program consoles. That’s where it’s important that you have the set construction go smoothly, because you don’t need to have much go wrong to lose half a day, and the knock on of that is significant. We were fortunate. We overestimated, and allowed for some overnight calls to build it, and fortunately after the first few days we were able to cancel those. Again, it saves money, and it means everyone isn’t so tired, and are a bit more focused on what they’re doing.
NL: What were the main challenges of integrating the lighting with the set?
NE: Just the lighting and the towers. Getting the lights up there, we can no longer get access to them, and then because the whole cyc at the back is curved, to fly the cyc, the gauze in front of it, and the lighting that’s in there, there are 16 fly bars involved. If you want to drop the lights in to service them, you have to drop in all 16. That’s a very slow and complex process – it takes more than an hour to drop them all in, and we don’t like to do that if we can avoid it – it just takes up way too much time.
NL: Any other big challenges?
NE: The other thing about this one is that the set dressing is quite detailed as well. (Pointing to the bar upstage) There’s a lot of detail that’s gone into that. Because the physical set is so big and heavy, and can’t change, the scenes are all changed by the set dressing that is tracked on and off.
NL: Is taking it apart almost as much fun as putting it up?
NE: It’s faster though. Our current estimate is that it’s 36 hours to get it out and into the trucks. We obviously don’t know that because there’s no precedent. That’s part of the fun with a new show. Like the cast, who are learning new lines and choreography, we’re learning a new set and how to make it work.
Images: (top) Naval Officers in front of the set. Photographer: Brian Geach & (lower) construction images courtesy of Nick Eltis.
Our Previous Coverage
An Officer and a Gentleman to Close
An Officer and a Gentleman Launched
Chat with Kate Kendall and Alex Rathgeber
Receive a FREE An Officer and a Gentleman The Musical Sampler CD with the current print edition of Stage Whispers.
The disc features five songs and three bonus music videos from An Officer and a Gentleman the Musical. Ben Mingay sings I'm Gonna Fly, Amanda Harrison sings If You Believe in Love the Way I Do and Wings of My Own, Josh Piterman and the company sing Halfway and Ben Mingay, Amanda Harrison, Alex Rathgeber and Kate Kendall sing Up Where We Belong.
Buy a copy or subscribe at www.stagewhispers.com.au/products